While the superb quality of products is and must always remain a number one priority in any production process optimization in the furniture industry, there are many other factors to consider. One of them is definitely cost optimization, which can help deliver the same excellent results with less invested funds. At the same time, a well-calculated and carefully planned cost optimization can also help shorten manufacturing times, improve the quality of results and help make the entire process a lot more sustainable. But in order to achieve all these benefits, it is important to approach the production process optimization carefully and reasonably.
Sustainability as an Essential Part of Our Brand’s DNA
At Skaza, we recognize that some of the biggest challenges our society and our planet are facing nowadays are closely connected to the environment, so we developed unique solutions to overcome those issues. Creating innovative products and building furniture components from sustainable materials has become our everyday task. Thanks to our vast experience and knowledge, we have been able to incorporate these materials into affordable solutions, thus creating sustainable products that manage to maintain the highest quality as well as keep the costs as low as possible.
Production Process Optimization in 5 Steps
Well-calculated and carefully planned production process optimization consists of five important steps, each playing a key part in finding the best possible solution.
Step #1: Problem Identification
The problem identification step is designed to comprise information related to the relevant response variables and control factors. This requires a group of experts, knowledgeable about the product who are able to make an informed decision regarding the process.
Step #2: Experiment Planning and Execution
This step focuses on exploring the technical aspects that need to be considered when making a decision regarding the experimental design.
Step #3: Modeling of Response Mean and Variance
This step mainly focuses on developing regression models for the mean and variance of responses, using one of the four available modeling techniques.
Step #4: Choice of Utility Function and Optimization Criteria
The choice of utility functions is primarily based on the criteria that need to be considered in the optimization process. This step focuses on choosing the correct utility functions in order to achieve the best possible optimization results.
Step #5: Optimization Proper
Once a suitable objective function (a utility function that combines responses and information that is relevant to them) is determined, a programming routine is performed to determine the settings for the control factors that best fit the optimization criteria. This final step thus enables a conclusion of the optimization process with the highest possible success rate.
Cutting Costs vs. Optimizing Costs – What Is the Difference?
While both processes, cutting costs as well as optimizing costs, clearly have the same goal, which is achieving more with fewer resources, there is an important difference in how a company can reach that result. While cutting costs focuses solely on reducing the financial input and disregards most other factors, a process of optimizing costs can also bring a number of other benefits. However, this process does require a deeper understanding of your business and customer’s needs as well as more time and resources, but the investment is definitely worth it in the end.
Cost optimization thus shifts and expands the definition of reducing costs, as it mainly focuses on developing and growing a business while also taking into account the ever-growing demand from customers to reduce their production costs.
Cost optimization requires careful planning and forecasting of both the production plant equipment as well as supply chain processes, increased focus on flexibility and agility, and willingness to slightly increase investment costs in the short term in order to achieve lower costs and better results in the long run.
Production Process Optimization for Lower Costs, Shorter Production Times and Better Quality of Products
We have already established that carefully planned production process optimization can help reduce production costs, but it also brings a number of other benefits. Optimization can also help shorten production times, thus enabling faster delivery and improving the final product's quality. And last but not least, production process optimization can also significantly improve the sustainability of the production process, which should definitely be one of the top priorities of every plastics manufacturer.
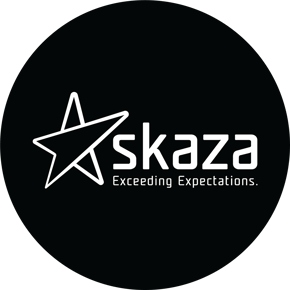