Overmolding is a process of combining various different materials, such as plastics and metals. Overmolding process offers a variety of important benefits, such as manufacturing products with multiple materials in a relatively simple way, lower costs in comparison to some other manufacturing methods and reduced need for product assembly. It often represents the best choice for a manufacturing method, especially for larger numbers of products.
Contact us to find out more. Send us an inquiry >>
However, the overmolding process in the plastic industry also has certain limitations that we need to keep in mind when selecting the best manufacturing method. For example, the overmolding process has excessive upfront costs, so a large number of products is needed to distribute these costs. At the same time, the overmolding process can also be time-consuming, expensive and quite complex. That is why it is important to weigh the advantages and disadvantages of using the overmolding process for each individual product.
The General Benefits of Overmolding Process
- Overmolding process combines various materials into one unified product, which can increase the product value.
- Overmolding process improves bonding and adhesion between parts.
- Overmolding process can add aesthetics, ergonomics and functionality, such as multiple colors, ergonomic grips, improved structure and mechanical strength.
- Overmolding process fully or partially reduces the need for post-processing and assembly, which can positively impact the cost of labor and reduce waste from the assembly, such as waste as a result of cutting, drilling, screwing the additional parts or waste from packaging of the additional parts.
- Overmolding process also reduces assembly time for the end consumer and additional parts for assembly.
Alternative Methods to Overmolding and Their Disadvantages
Apart from the overmolding process, there are also a number of other options used for insertions:
- Ultrasonic welding, which is a process of thermally joining components with high frequency ultrasonic acoustic vibrations.
- Heat staking is a method of insertion by using a thermal tip and insert nut. This process is similar to overmolding; however, the end result is weaker due to less efficient bonding.
- Cold staking is a method of insertion by force. It can cause material stress and cracks.
- Fastening is a less reliable method due to insert nut thread fatigue or damage. However, the fastener is exposed to less stress because the bonding is weaker between the insert nut and thermoplastic material, which results in more flexibility and dampening.
And how does the cost of the methods mentioned above compare to the cost of the overmolding process? Overall, overmolding is the most expensive method in terms of implementation, but on the other hand, it eliminates the cost of assembly as well as ensures the quality and strength of produced parts, so it is usually the most cost-efficient method in the long run. The downsides of the overmolding process are longer cycle times and the fact that the stronger the bonding between the insert and thermoplastic material, the more rigid the insert, which exposes the fastener to more stresses.
Case Study: Overmolding Process in Manufacturing a Chair
One of our flagship products in the field of overmolding process is the plastic chair, manufactured for one of our clients. For this chair, the clients did not specifically request overmolding, but we chose it nonetheless. The main reasons for this were the following:
- Consistency and reliability of the process
- Improved control over quality and fewer missing parts
- Fewer complaints related to the produced and sold parts
- Less manual and human labor
We created a plastic chair with over-molded insert nuts onto which the metal legs are fastened. We also paid special attention to the design of the insert itself, as we were aware of its importance. Optimally, end-cap inserts, produced with good heat-conducting metal, such as aluminum, are recommended. The overall shape of the insert should be aimed towards increasing surface area and thus increasing the bonding strength. Features such as ribs or roughened/textured surfaces are added to achieve better bonding. All this helps to create a sturdy, high-quality end product that our clients were very satisfied with.
Chosen by Skaza, Recognized by Our Clients
We already mentioned that in the beginning, the process of overmolding was not specifically required by our client, but we chose the process because of all the above-mentioned benefits. However, the final product received such excellent feedback that our client began demanding that overmolding should become the standard method of use. Consequently, all of the other suppliers had to implement the system that our team at Plastika Skaza first used for production.
Contact Us and Let Us Help You Find the Best Solution for Your Product
We always strive to look for the best solution for our clients’ products and we look forward to hearing from you and working together on creating another successful business story.
Looking for a partner who will manage high demands in manufacturing plastic products? Get a quote and become our partner.
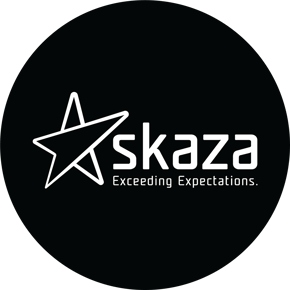