It should go without saying that the only workplace good enough for our employees is a safe one. At Skaza, we are continually revaluing every element of our workspace, generating a safe and creative environment sparking with new ideas.
The backbone of our commitment to developing such a productive atmosphere is the never-ending process optimization, resulting in a constant rise of efficiency and, even more importantly - a safer place for everyone.
A great example of a successful process optimization in our plastic industry that brought us closer to achieving our risk-free plastic manufacturing goals has recently been performed in our furniture industry department. Soon after we acquired a ten-year-old tool with lower performance capability for producing high-quality office chair components from a long-term partner, we realized that this unit's manufacturing process does not meet our high safety standards.
Demanding high standards of our production process
It didn’t take us long to apprehend that in order to sustain top-quality production on the newly obtained machine, we need to invest in its upgrade. Moreover, our operators were exposed to safety hazards during the manufacturing process, which proved to be even more challenging than maintaining the high standards we like to affiliate our products with. The principal problem proved to be in the so-called injection gate points, whose sharp edges presented a cutting risk to the operators. Normal injection point management was not an option for such an elaborate component as it did not yield high-enough quality of the manufactured product for our customers. Furthermore, this method did not align with our process optimization policy of keeping production line waste to a minimum.
In order to improve sharp injection points removal after molding, we needed to implement additional heat treatment to the production process. This required the implementation of new equipment from our engineers, which added an extra step, proving beneficial when managing sharp injection gates.
However, this upgrade didn’t come without further hiccups. Heat treatment presented a new, even higher risk to the operators who were now exposed to the danger of being burned. With the implementation of this process, the product's quality elevated and proved acceptable to the customer.
However, this extra step had a negative effect on our production, as the volume of waste actually grew and manufacturing costs increased. Besides, the process's stability was unreliable, as there could be a risk of producing lower-quality products due to the human factor. All these new challenges needed our immediate attention if we were to smooth out the production process for good.
To effectively approach the health hazard challenge, our engineers first had to carry out mould modification, which then allowed them to implement a pneumatic hot nozzle.
This innovative upgrade ensured a clean injection point without presenting any burn risk to the operators. Furthermore, with additional modifications to the process optimization, we decreased the production scrap rate from 7% down to only 2%, which yielded much lower material waste.
Feeling accomplished by introducing these pioneering tools that resulted in further optimization of our production process and severe health hazard reduction, we are confidently stepping towards new challenges in achieving high-set goals and exemplary plastic manufacturing practices.
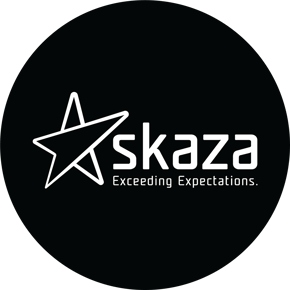